The Flying Clothes Peg
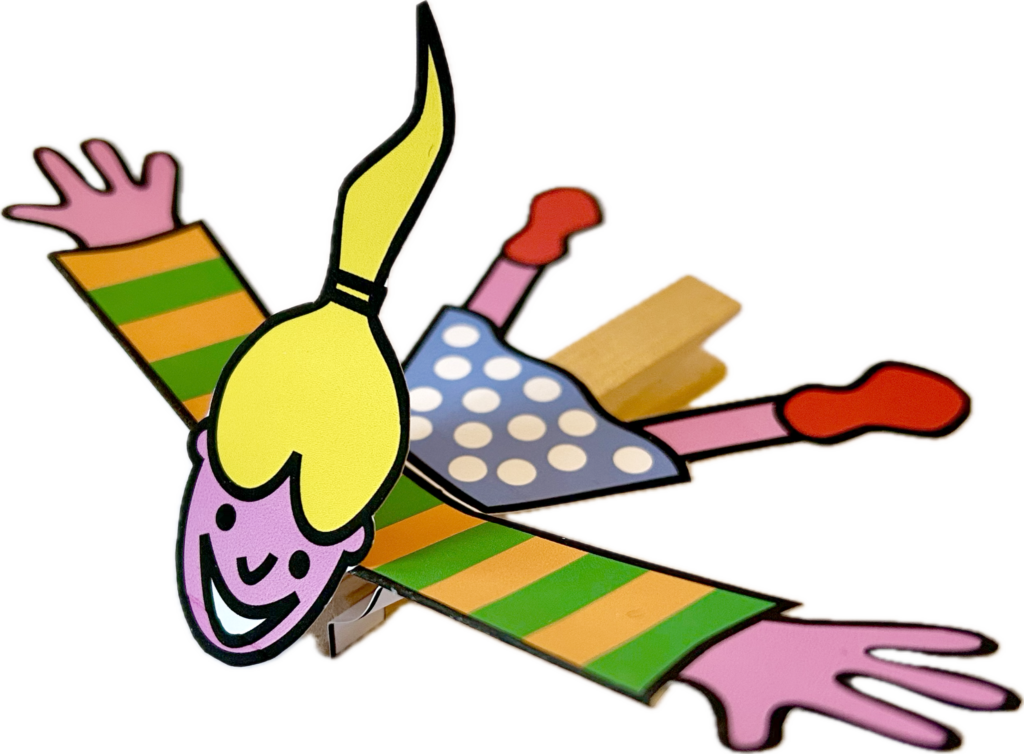
Introduction
I was recently asked to produce some instructions for a moving butterfly using a clothes peg/pin to accompany a small exhibition of automata at the excellent Imaginata museum in Jena, Germany (https://imaginata.de). After the visitors have had fun interacting with the automata on display, the idea is that they should have the opportunity of making their own, very simple automata, on a table in the exhibition space. Obviously it shouldn’t cost too much, whilst showing that it’s not rocket science to get things moving, and that you can use everyday objects which aren’t too hard to find.
Here’s what I came up with.
The Materials
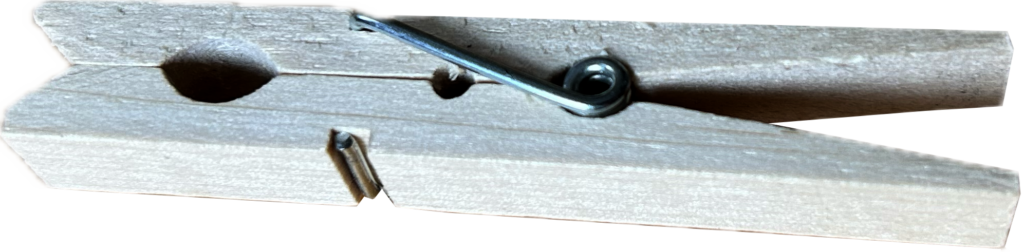
If your clothes peg is a different size, you may have to scale the pattern to match.
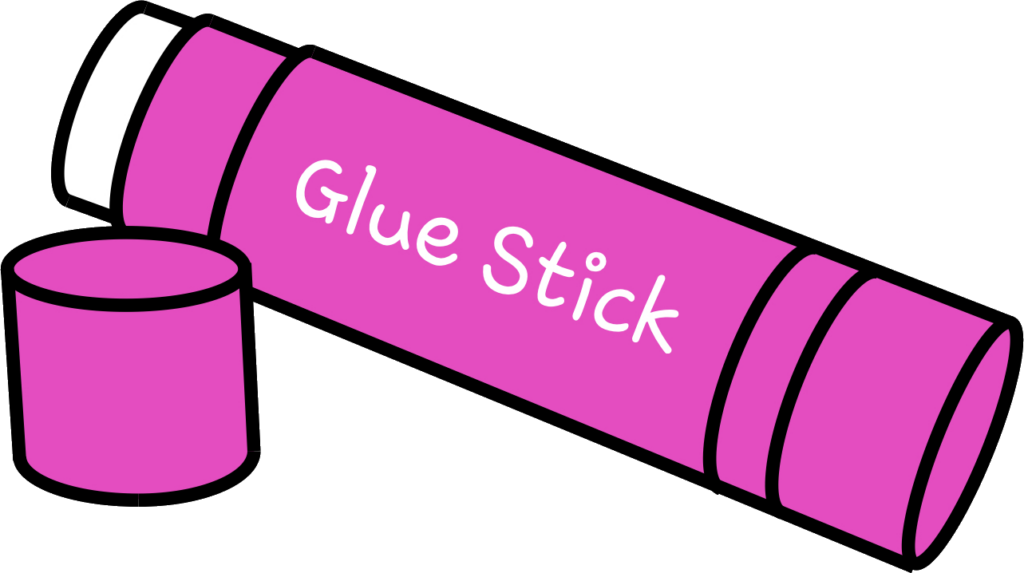
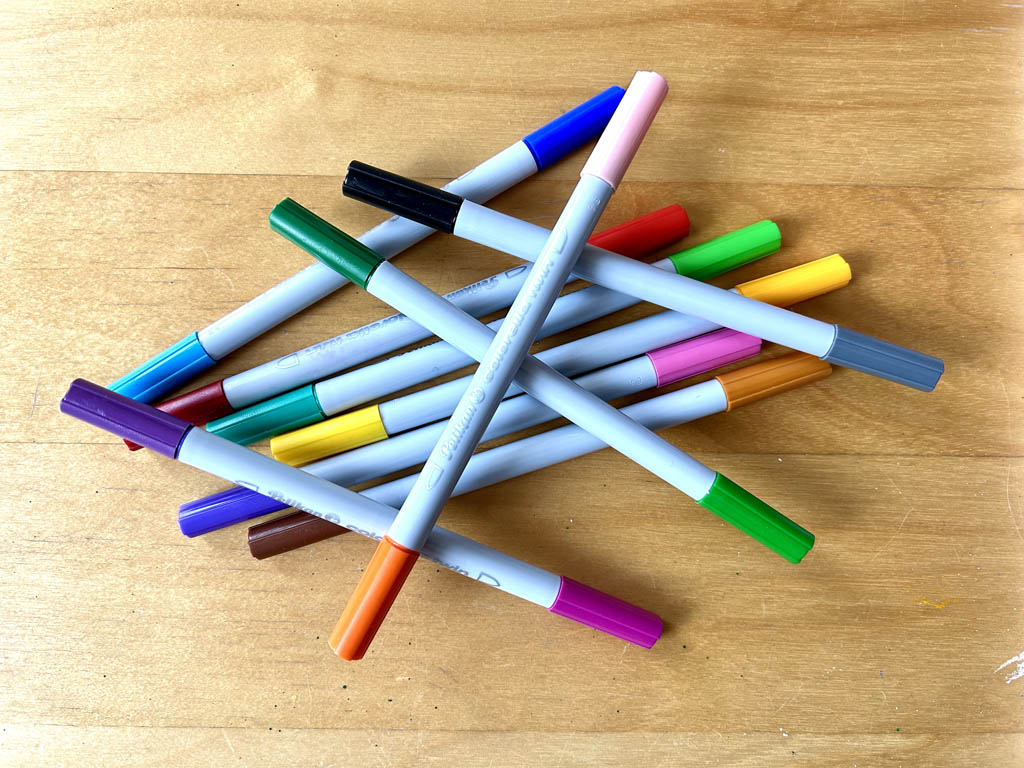
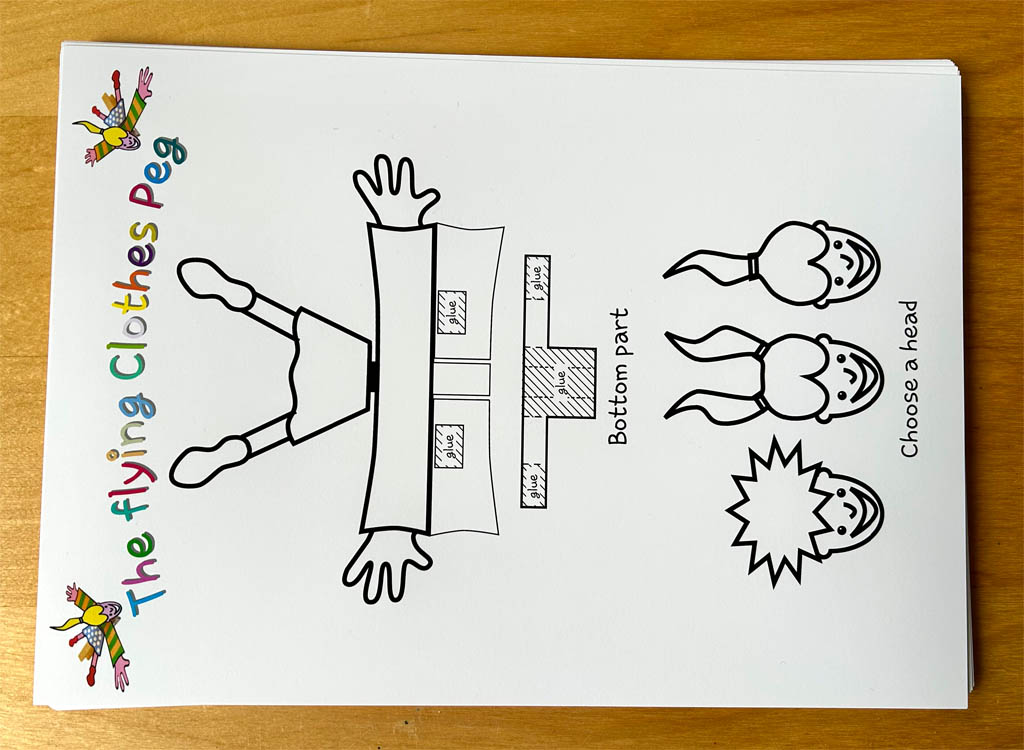
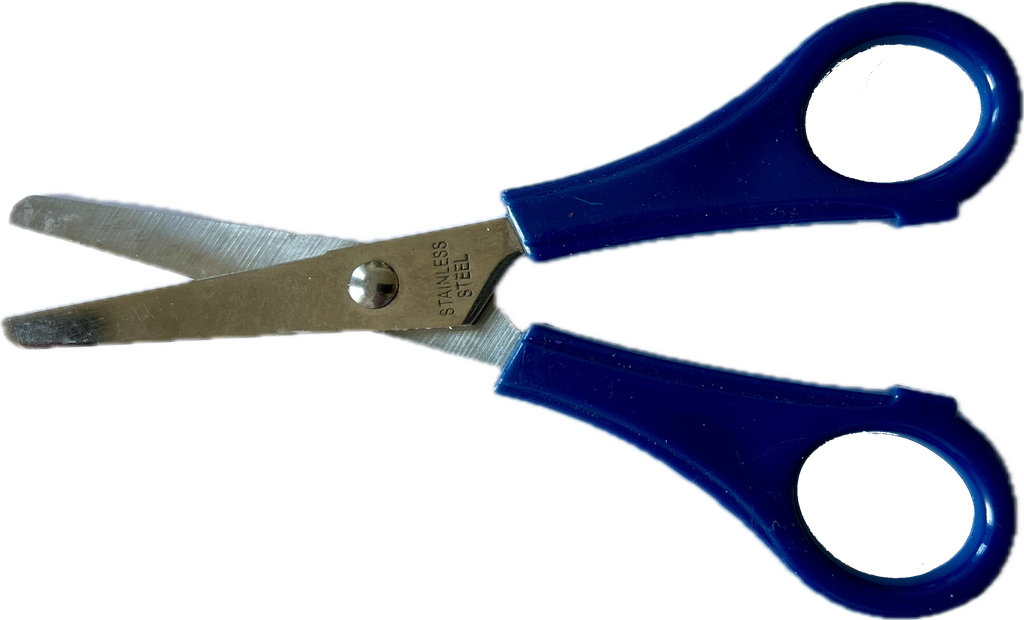
The Pattern
You can download the pattern in PDF format here (ADD LINK), or in JPEG format here (ADD LINK). If you don’t use A4 paper, you could edit the JPEG file to fit on your paper size. The same applies if you want to use a language other than English. When printing, use at least 175 g paper.
Instructions
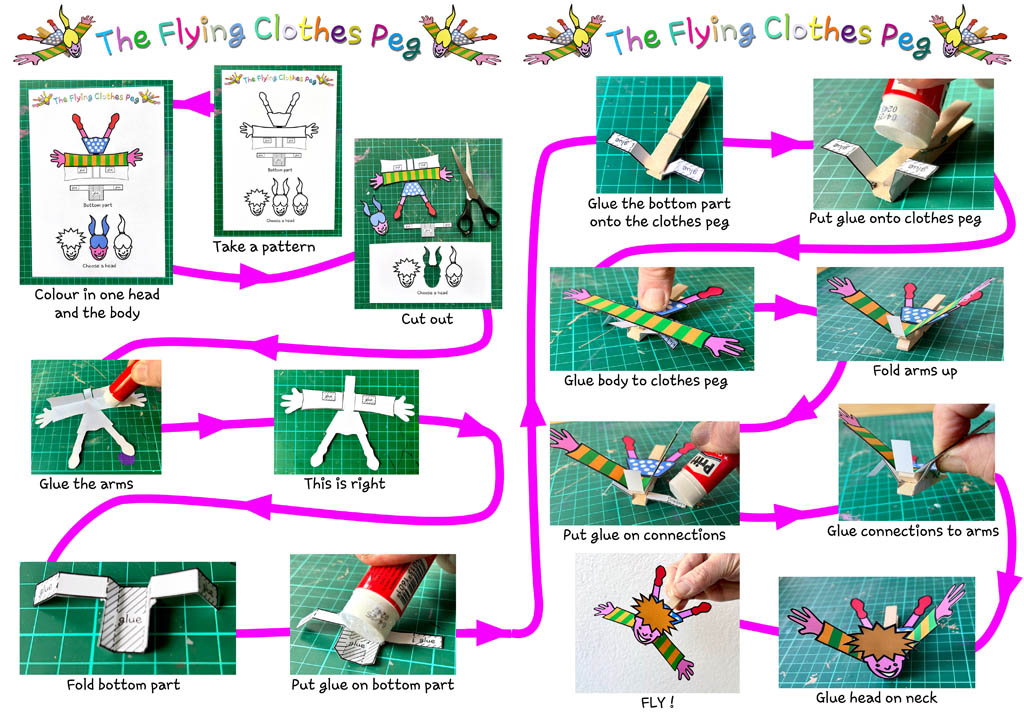
There are two A4 pages of instructions which you can download in PDF formet here (ADD TWO LINKS), or in JPEG format here (ADD TWO LINKS). If you don’t use A4 paper, you could edit the JPEG files to fit on your paper size. The same applies if you want to use a language other than English. Note that I folded the arms to make them stiffer and flap more convincingly.
Testing
Before sending the instructions off to the Imaginata in Jena, I asked a 9 year old to have a go, which she was very happy to do. I had a finished example to show her and she seemed to immediately understand the idea. Colouring in the figure took a while as she considered what her best friend looked like and what colour clothes she wore. Filled with enthusiasm, she wanted to colour in both sides of the A4 pattern, holding the pattern against a window pane to be able to see the pattern through the paper. I then noticed that I should have suggested felt-tip pens instead of the waxy crayons which she had chosen herself. I doubted that the waxy surface would glue properly, so I helped her to avoid the areas where glue was required. She was happy with the finished product and decided to take it to her best friend’s birthday the very next day, together with a kit of parts for her friend to try it out herself.
What Happened to the Butterfly?
I was asked to make a butterfly, so what happened? Scouring the Internet before starting, to see if someone had already produced instructions, of course I found a video on Youtube. Looking at it, I thought that it was easy to make, if a bit uninteresting. The maker had also used a hot-glue gun which I considered too dangerous and messy for the young or the young at heart to use unsupervised. A glue stick seems to be a good alternative in this case, even if a few seconds of patience is required for it to stick sufficiently. So, I made a flying girl instead of a butterfly and my contact at the museum was happy to accept it, after making one himself to try it out.
The pattern could be modified for all sorts of things. A butterfly, a bat, a dragon, a boy, a bird, a bee, a stingray, a dragonfly anything where flapping is required. I did think about a super-hero, but can you really imagine superman flapping his arms to fly around and save the world? How realistic would that be! What would you make?
Reflections
There is a wide range of automata, that people make using clothes pegs. Often they use bits of wire or straightened paper clips. Sometimes holes are drilled. For this design we don’t need wire cutters or a drill. An all paper design might be possible but I’m guessing that it would be more complicated. A clothes peg is also something very domestic and I think it adds a bit of charm.
Video
URL https://www.youtube.com/watch?v=P8_O1J-BRIA